The Evolution and Importance of Precision Plastic Molding in Modern Manufacturing
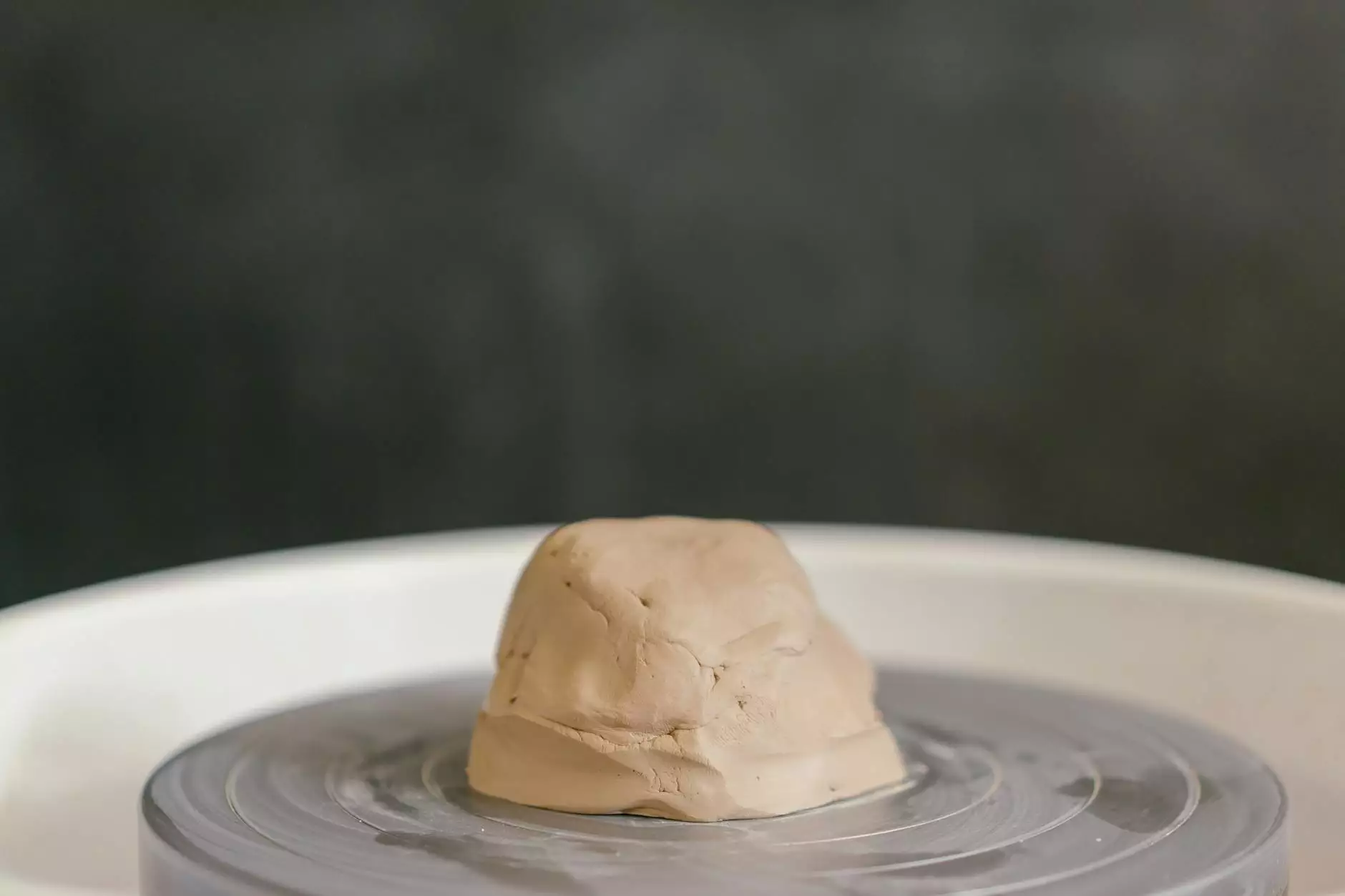
Precision plastic molding has become a cornerstone of modern manufacturing, offering unparalleled efficiency, accuracy, and customization. As industries continue to evolve, the demand for high-quality plastic components grows, making precision plastic molding an indispensable process.
Understanding Precision Plastic Molding
At its core, precision plastic molding refers to the manufacturing process that utilizes customized molds to create exact plastic parts with minimal tolerances. This technique enables the production of complex shapes and sizes tailored to specific applications across various industries.
Key Characteristics of Precision Plastic Molding
- High Tolerances: Ability to produce parts with tolerances as tight as ±0.001 inches.
- Complex Geometries: Capability to manufacture intricate designs which would be difficult with traditional methods.
- Material Versatility: A wide range of plastics can be used, including thermoplastics, thermosets, and elastomers.
- Efficiency: High-speed production with repeatable processes that reduce cycle times.
Benefits of Precision Plastic Molding for Businesses
Businesses today are constantly on the lookout for ways to enhance their production methods and improve product quality. Here are some compelling benefits of incorporating precision plastic molding into your operations:
1. Cost-Effectiveness
While the initial setup cost may be higher than traditional methods, the long-term savings realized through reduced material waste, lower labor costs, and minimized lead times make precision plastic molding a cost-effective choice for many businesses.
2. Enhanced Product Quality
The ability to produce parts with high precision and consistency means that products have fewer defects and meet stringent quality standards, leading to improved customer satisfaction and reduced return rates.
3. Speedy Production Process
With advances in technology, precision plastic molding can operate at high speeds, enabling companies to respond quickly to market demands and reduce time-to-market for new products.
4. Design Flexibility
Manufacturers can easily modify designs without significant investments in new tooling, allowing for rapid prototyping and testing, which is crucial in industries where innovation is key.
Applications of Precision Plastic Molding
The versatility of precision plastic molding makes it applicable across a myriad of industries. Here are some significant areas where this technology is utilized:
1. Medical Industry
In the medical field, precision is paramount. From surgical instruments to housing for medical devices, precision plastic molding ensures that components are sterile, safe, and adhere to strict regulatory standards.
2. Automotive Sector
Automotive manufacturers depend on precision plastic parts for everything from dashboards and controls to internal components. Lightweight, durable plastics help improve fuel efficiency and vehicle performance.
3. Consumer Electronics
With the rapid advancement of technology, consumer electronics require compact and lightweight designs. Precision plastic molding helps create these components with the necessary durability and aesthetic appeal.
4. Aerospace Engineering
Aerospace applications demand the lightest possible materials while maintaining strength and performance. Precision plastic molding provides solutions for components in critical structures and systems.
Choosing the Right Precision Plastic Molding Manufacturer
When selecting a manufacturer for your precision plastic molding needs, consider the following criteria:
1. Experience and Expertise
Choose a manufacturer with a proven track record in the industry. Experience often correlates with knowledge of advanced techniques and material properties, which is essential for delivering high-quality products.
2. Range of Services
Look for manufacturers that offer a comprehensive range of services, including design assistance, prototyping, production, and post-production services like assembly and packaging.
3. Technological Capabilities
Advanced machinery and software capabilities can significantly impact the efficiency and precision of the molding process. Ensure that the manufacturer invests in the latest technology.
4. Quality Assurance Processes
A robust quality control system is vital. Manufacturers should have an established process for testing and inspecting parts to ensure they meet required specifications.
Future Trends in Precision Plastic Molding
The landscape of precision plastic molding is continuously evolving, influenced by trends in technology and consumer demand. Some notable future trends include:
1. Sustainable Practices
As the world becomes more environmentally conscious, the shift towards sustainable materials and processes is growing. Manufacturers are exploring biodegradable plastics and recycling methods that reduce waste.
2. Automation and AI Integration
Automation and artificial intelligence are set to revolutionize the industry. From automated quality control to predictive maintenance systems, these cutting-edge technologies can enhance efficiency and lower costs.
3. Increased Customization
With advancements in technology, there will be greater demand for customized products. This shift will push manufacturers to adopt flexible molding processes that allow for shorter runs of highly customized designs.
Conclusion
In conclusion, precision plastic molding plays a critical role in various industries, enabling businesses to produce high-quality, reliable products efficiently. By understanding its benefits, applications, and future trends, companies can better leverage this technology to enhance their operations and meet customer demands.
Whether you're part of the automotive sector, medical industry, or any other field that relies on precision manufacturing, implementing precision plastic molding can transform your production line and deliver superior results. Embrace the future of manufacturing with confidence and watch your business thrive.